Custom Cutting Tools
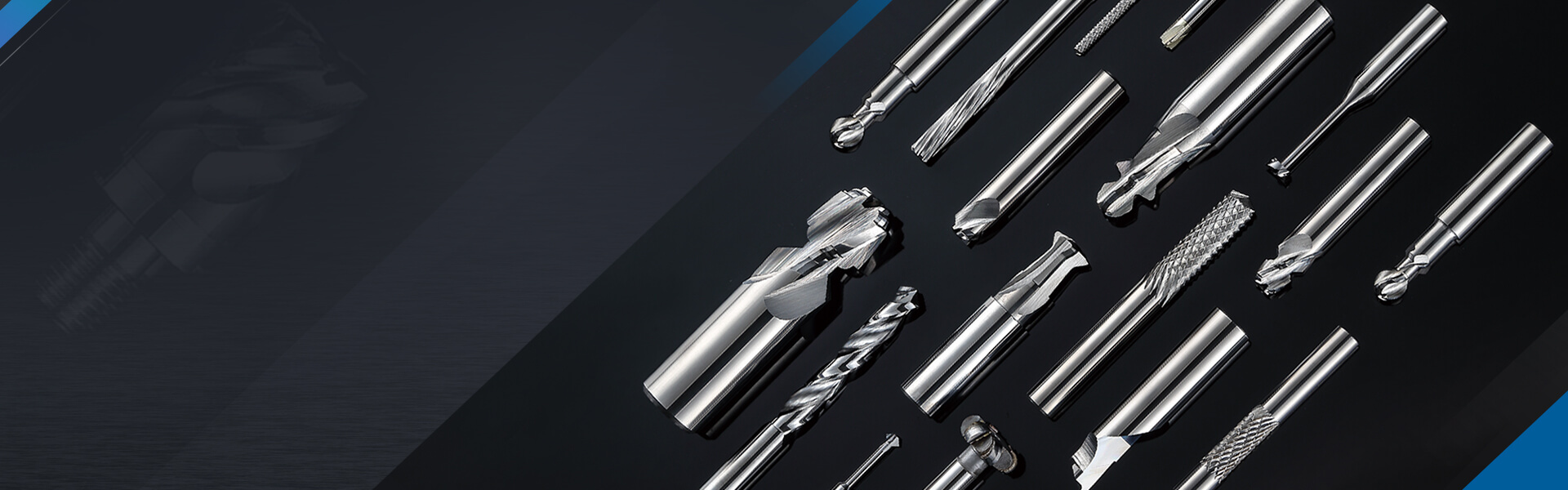
Junyi Tungsten Steel Tools provides comprehensive customized cutting tool solutions
Customized cutting tools are designed according to specific needs or special applications. Compared to standardized tools, customized tools offer a more precise and efficient cutting experience, thereby increasing productivity and reducing costs. Since the needs of each production environment and product are different, customized cutting tools can be designed according to specific materials, machining requirements, and operating conditions to ensure optimal processing results.
Advantages of Customized Cutting Tools
-
Increased EfficiencyCustomized tools can be optimized for specific machining processes, thereby improving machining efficiency. This means that more machining tasks can be completed in the same amount of time, reducing production time and costs.
-
Extended Tool LifeSince customized tools are specifically designed for certain applications, they can reduce wear and breakage, thereby extending the tool’s service life. This not only saves on the cost of purchasing new tools but also reduces downtime caused by tool replacement.
-
Improved Product QualityPrecise cutting tools can ensure better processing quality, reducing defects and rework rates. This is especially important for industries requiring high precision and quality.
-
Reduced Production CostsBy increasing efficiency and reducing tool wear, customized tools can significantly lower production costs. Although the initial cost may be higher, it is a costeffective investment in the long run.
Application Scope of Customized Cutting Tools
Customized cutting tools are widely used in various industries for component processing:
Design Process of Customized Cutting Tools
Designing customized cutting tools involves the following stages:
-
Requirement AnalysisCommunicate with the customer to understand the specific needs and machining environment. This step is crucial as it determines the direction and key parameters of the tool design.
-
Material SelectionChoose suitable tool materials based on the properties of the machining materials. Tungsten steel is often selected due to its high hardness and wear resistance.
-
Tool DesignBased on the requirements and materials, design the shape, size, and tooth arrangement of the tool.
-
ManufacturingManufacture the tool according to design drawings, perform necessary treatments, and inspections to ensure the tool meets design requirements.
-
Testing and AdjustmentTest the tool’s performance in actual production and make adjustments and optimizations based on the results.
-
Mass ProductionOnce the tool design passes testing and adjustments, mass production can begin to meet demand.
Junyi Tungsten Steel Tools’ Expertise
Junyi Tungsten Steel Tools has extensive experience and expertise in the field of customized cutting tools.
We provide onestop services from requirement analysis to final product delivery, ensuring that customers receive satisfactory tool solutions.
With advanced manufacturing equipment and a highquality R&D team, Junyi Tungsten Steel Tools can quickly respond to market changes and customer needs, offering highquality, highperformance customized cutting tools. Feel free to contact us at any time.
Customized Cutting Tools
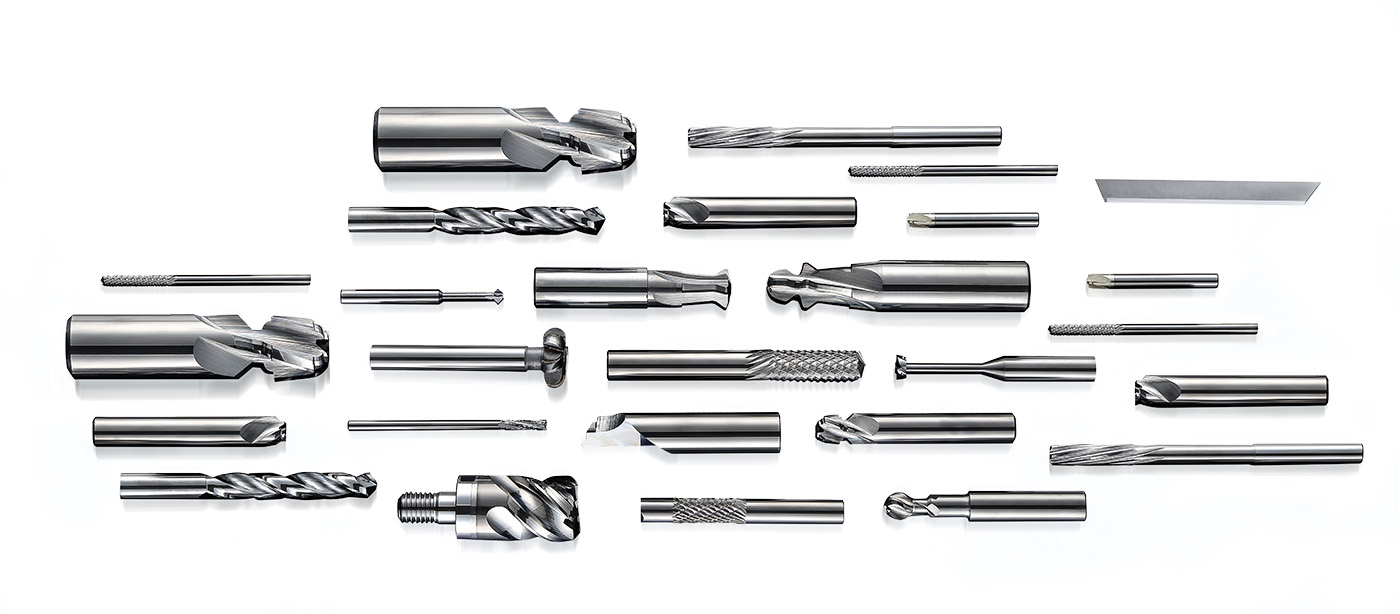